Recognizing What is Porosity in Welding: Reasons and Solutions
Wiki Article
Understanding Porosity in Welding: Discovering Reasons, Effects, and Prevention Methods
As specialists in the welding market are well conscious, recognizing the reasons, effects, and prevention methods related to porosity is essential for achieving durable and trusted welds. By delving into the root triggers of porosity, analyzing its damaging effects on weld quality, and exploring reliable avoidance approaches, welders can enhance their understanding and skills to generate premium welds regularly.Common Root Causes Of Porosity
Porosity in welding is mainly brought on by a combination of elements such as contamination, inappropriate protecting, and poor gas insurance coverage during the welding process. Contamination, in the kind of dirt, oil, or rust on the welding surface area, develops gas pockets when heated, bring about porosity in the weld. Inappropriate shielding happens when the protecting gas, typically used in processes like MIG and TIG welding, is incapable to completely secure the liquified weld pool from responding with the surrounding air, causing gas entrapment and succeeding porosity. Additionally, inadequate gas insurance coverage, frequently because of wrong flow prices or nozzle positioning, can leave components of the weld unprotected, permitting porosity to form. These elements collectively add to the formation of gaps within the weld, damaging its integrity and potentially causing structural problems. Recognizing and addressing these usual causes are crucial actions in protecting against porosity and ensuring the top quality and strength of welded joints.Impacts on Weld High Quality
The existence of porosity in a weld can substantially jeopardize the overall high quality and honesty of the bonded joint. Porosity within a weld produces spaces or cavities that damage the framework, making it extra vulnerable to fracturing, deterioration, and mechanical failure. These gaps serve as anxiety concentrators, reducing the load-bearing ability of the weld and boosting the chance of early failure under applied anxiety. In enhancement, porosity can also offer as potential websites for hydrogen entrapment, more worsening the degradation of the weld's mechanical residential or commercial properties.Moreover, porosity can impede the performance of non-destructive testing (NDT) strategies, making it testing to spot other issues or gaps within the weld. This can cause significant security concerns, specifically in essential applications where the structural integrity of the bonded elements is paramount.
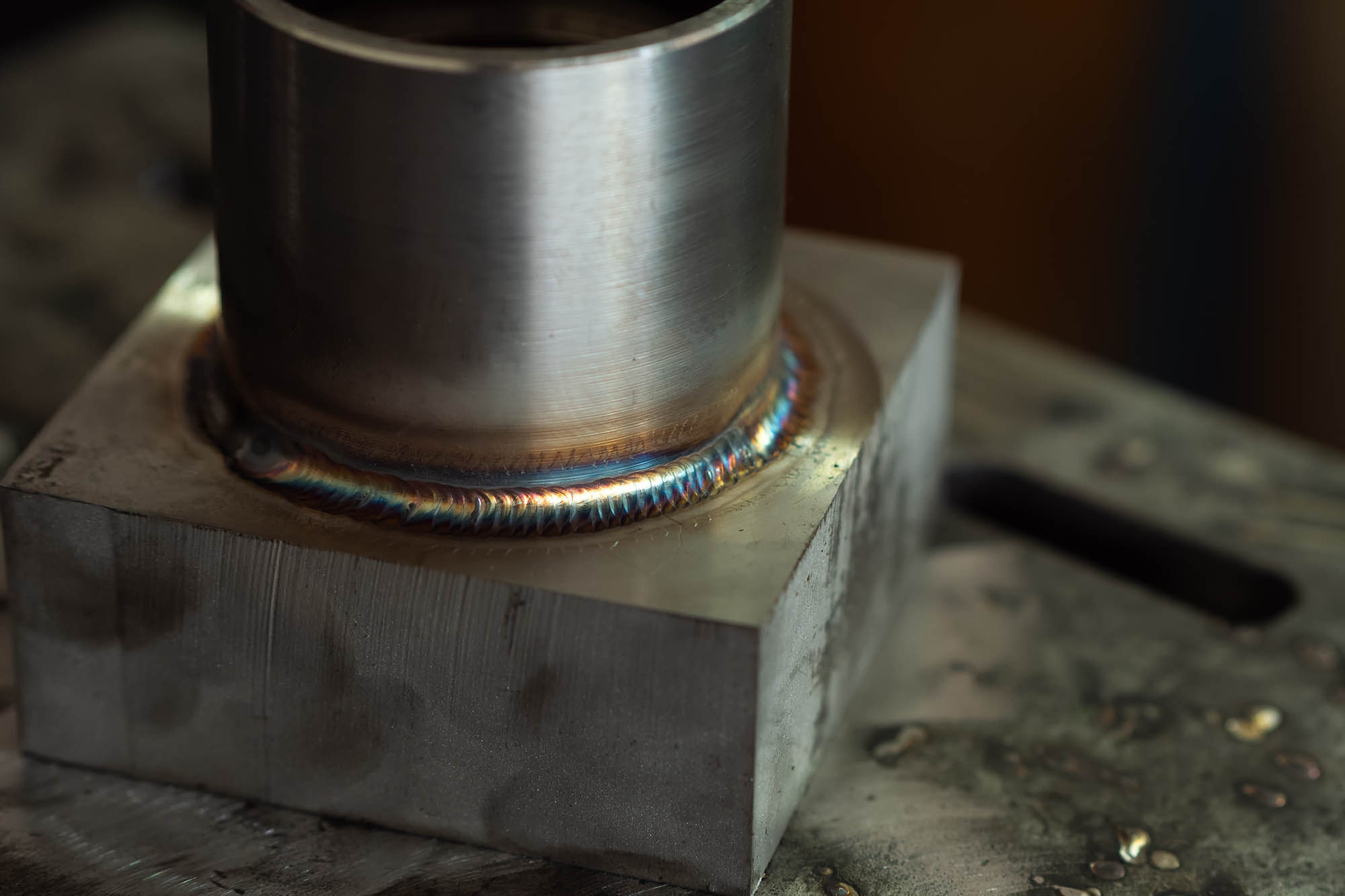
Prevention Techniques Summary
Offered the damaging influence of porosity on weld high quality, efficient avoidance strategies are essential to keeping the structural stability of welded joints. Furthermore, selecting the proper welding parameters, such as voltage, existing, and travel speed, can help reduce the danger of porosity development. By including these prevention methods into welding practices, the occurrence of porosity can be significantly minimized, leading to stronger and a lot more dependable hop over to these guys welded joints.Importance of Proper Protecting
Appropriate shielding in welding plays a critical role in preventing atmospheric contamination and making certain the honesty of welded joints. Shielding gases, such as argon, helium, or a mixture of both, are typically used to safeguard the weld pool from reacting with components airborne like oxygen and nitrogen. When these responsive components enter contact with the hot weld swimming pool, they can create porosity, resulting in weak welds with minimized mechanical homes.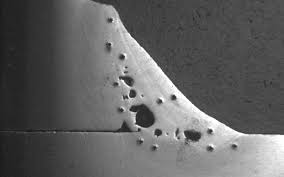
Poor shielding can cause various defects like porosity, spatter, and oxidation, endangering the architectural honesty of the bonded joint. Consequently, adhering to correct securing practices is necessary to create top quality welds with very little issues and ensure the longevity and integrity of the bonded parts (What is Porosity).
Tracking and Control Techniques
How can Continue welders successfully keep an eye on and control the welding procedure to make sure optimum outcomes and protect against issues like porosity? By continuously checking these variables, welders can determine discrepancies from the perfect problems and make instant modifications to avoid porosity development.
Furthermore, implementing correct training programs for welders is important for keeping track of and controlling the welding procedure efficiently. What is Porosity. Informing welders on the value of keeping consistent parameters, such as proper gas shielding and travel rate, can help prevent porosity concerns. Normal assessments and qualifications can likewise guarantee that welders excel in surveillance and regulating welding processes
Moreover, making use of automated welding systems can enhance surveillance and control capacities. These systems can precisely manage welding specifications, minimizing click for more info the possibility of human mistake and making sure consistent weld high quality. By incorporating innovative monitoring modern technologies, training programs, and automated systems, welders can effectively monitor and control the welding process to reduce porosity issues and attain high-grade welds.
Final Thought

Report this wiki page